Crosscutting large panels requires a systematic approach focused on precision, safety, and repeatability. This guide will walk through exactly what you need to know for consistently accurate cuts.
Understanding Panel Crosscutting Fundamentals
The key to successful crosscutting lies in two critical elements:
- Complete panel support throughout the entire cutting process
- A precisely squared and secured guide rail system
A recent review from Jeff R. illustrates this perfectly: "After switching to a proper support and guide rail system, I finished an entire 8'x16' media center project requiring over 25 sheets of plywood with perfect accuracy. The difference in cut quality and consistency was remarkable."
Essential Equipment Requirements
The Work Surface
Your workbench must provide:
- Minimum depth of 24.41 inches for adequate panel support
- 20mm dog holes for secure accessory mounting
- T-track integration for flexible clamping options
- Adjustable legs for perfect leveling on uneven surfaces
Guide Rail System Components
For precision cuts, you need:
- Guide Rail Brackets that can maintain square without constant readjustment
- SpiRail dogs for consistent rail positioning
- Track Stars or Outriggers for extended material support
- A parallel guide system for repetitive cuts
Setting Up for Large Panel Crosscuts
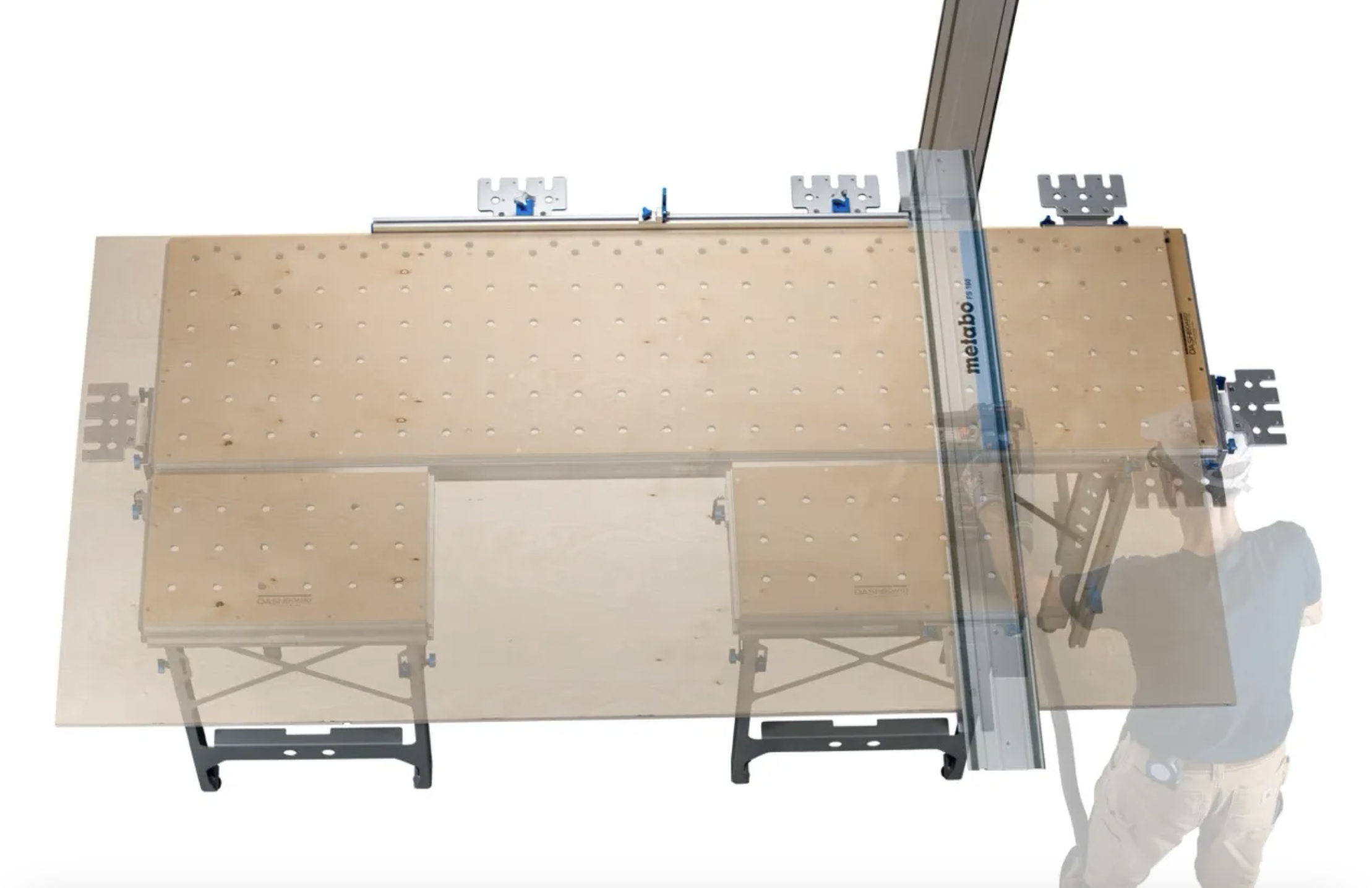
1. Workbench Configuration
- Install/set up Guide Rail Brackets
- Position Track Stars or Outriggers to support panels
- Verify bench is flat and/or level using adjustable feet
- Ensure all mounting hardware is properly tightened
2. Guide Rail Preparation
Critical steps include:
- Installing SpiRail dogs in your track saw rail
- Verifying square alignment using a reliable reference
- Setting proper blade depth for your material
3. Panel Support Setup
Proper support requires:
- Even spacing of support points every 24-36 inches
- Height matching between all support surfaces
- Clearance for offcuts to prevent binding
- Stability verification before cutting
Advanced Cutting Techniques
Making the Perfect Cut
- Initial Positioning:
- Align panel against squared fence
- Set stops for repetitive cuts
- Verify measurements on both ends
- Cutting Process:
- Make a shallow scoring cut first (1-2mm depth)
- Complete the cut in one smooth motion
- Maintain consistent feed rate
- Support offcut throughout the entire cut
- Quality Verification:
- Check square immediately after cut
- Measure both ends for consistency
- Verify surface finish quality
- Test fit if making multiple matching pieces
Common Challenges & Solutions
Challenge: Inconsistent Cut Depth
Solution:
- Use proper blade height setting
- Ensure rail stays firmly seated
- Verify no debris under rail
Challenge: Cut Line Tearout
Solution: Combined approach:
- Score cut first
- Choose appropriate blade tooth count
- Control feed rate
Measuring and Layout Tips
Using Reference Edges
- Establish a primary reference edge
- Use Flip Stops or Parallel Guides for repeatability
- Account for blade kerf in measurements
Setting Up Stops
Secure firmly to fence
- Check measurement accuracy
- Test with scrap material
System Integration and Workflow
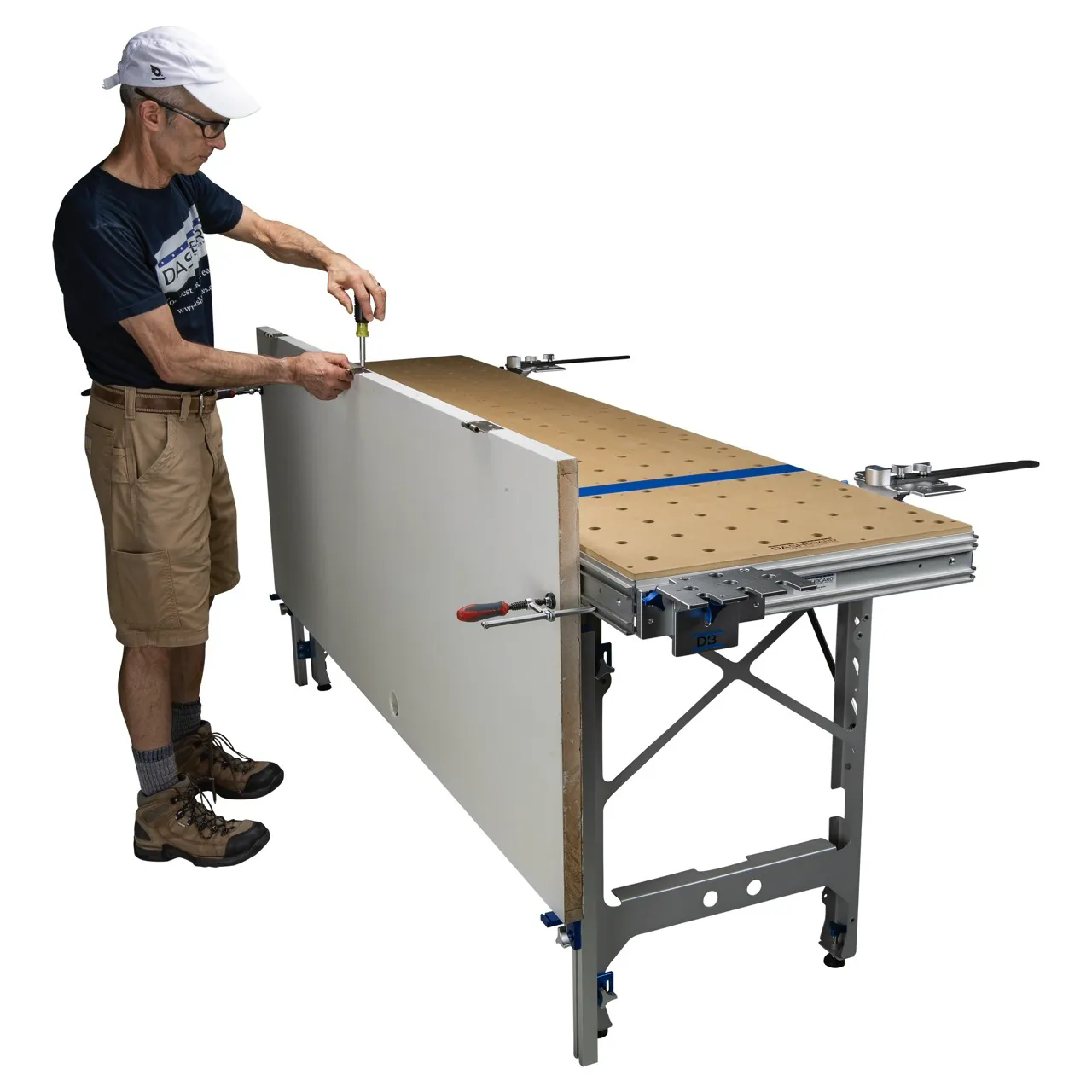
Creating an Efficient Setup
- Organize your workspace:
- Position bench for maximum material flow
- Arrange tools within easy reach
- Maintain clear access to all adjustment points
- Material handling:
- Stage panels for efficient processing
- Plan cut sequence to minimize waste
- Maintain support for large offcuts
- Consider material grain direction
Practical Tips from Experience
Based on extensive testing and professional feedback:
- Always verify square before starting production cuts
- Use integrated measurement systems when possible
- Keep support surfaces clean and debris-free
- Check and maintain tool calibration regularly
- Document successful setups for repeatability
Advancing Your Capabilities
To achieve professional-level results:
- Invest in quality core components:
- Solid workbench system
- Precise Dash-Board Guide Rail Brackets
- Reliable track saw
- Proper support accessories
- Practice systematic approach:
- Follow consistent setup procedures
- Document successful techniques
- Test new methods on scrap first
- Maintain equipment carefully
Next Steps
To implement these techniques effectively:
- Evaluate current setup against these requirements
- Identify specific equipment needs
- Develop a systematic approach to cuts
- Practice these methods to build consistency
For more information on professional-grade panel processing equipment, visit dashboardpws.com.
Frequently Asked Questions About Crosscutting Large Panels
What's the minimum equipment needed for accurate panel crosscuts?
Three essentials: A stable workbench (minimum 24" deep), a track saw with guide rail, and proper panel supports.Dash-Board Guide Rail Brackets are strongly recommended. While you can make cuts with less, these core items ensure reliable results.
How do I prevent tearout when crosscutting plywood?
Make a scoring cut first (1-2mm deep), use a crosscut or combination blade designed for the material in use, and maintain a consistent feed rate.
What's the best way to handle full 4x8 sheets alone?
Use support systems with Outriggers or Track Stars positioned every 24-36 inches. Place one end on your workbench, then walk the other end up while supports hold the weight. Use a panel carrier for transport. Think about leverage and balance points.
How do I ensure my cuts stay perfectly square?
Mount Guide Rail Brackets securely, follow our setup procedure, and verify with a test cut. Quality brackets maintain position without constant adjustment. Check square periodically and always verify after moving your setup.
What size workbench do I really need for panel processing?
Your workbench should be at least 24.41 inches deep with a practical minimum length of 60 inches. However, proper support extensions or Outriggers are more important than bench size; they allow successful panel processing even on shorter benches.